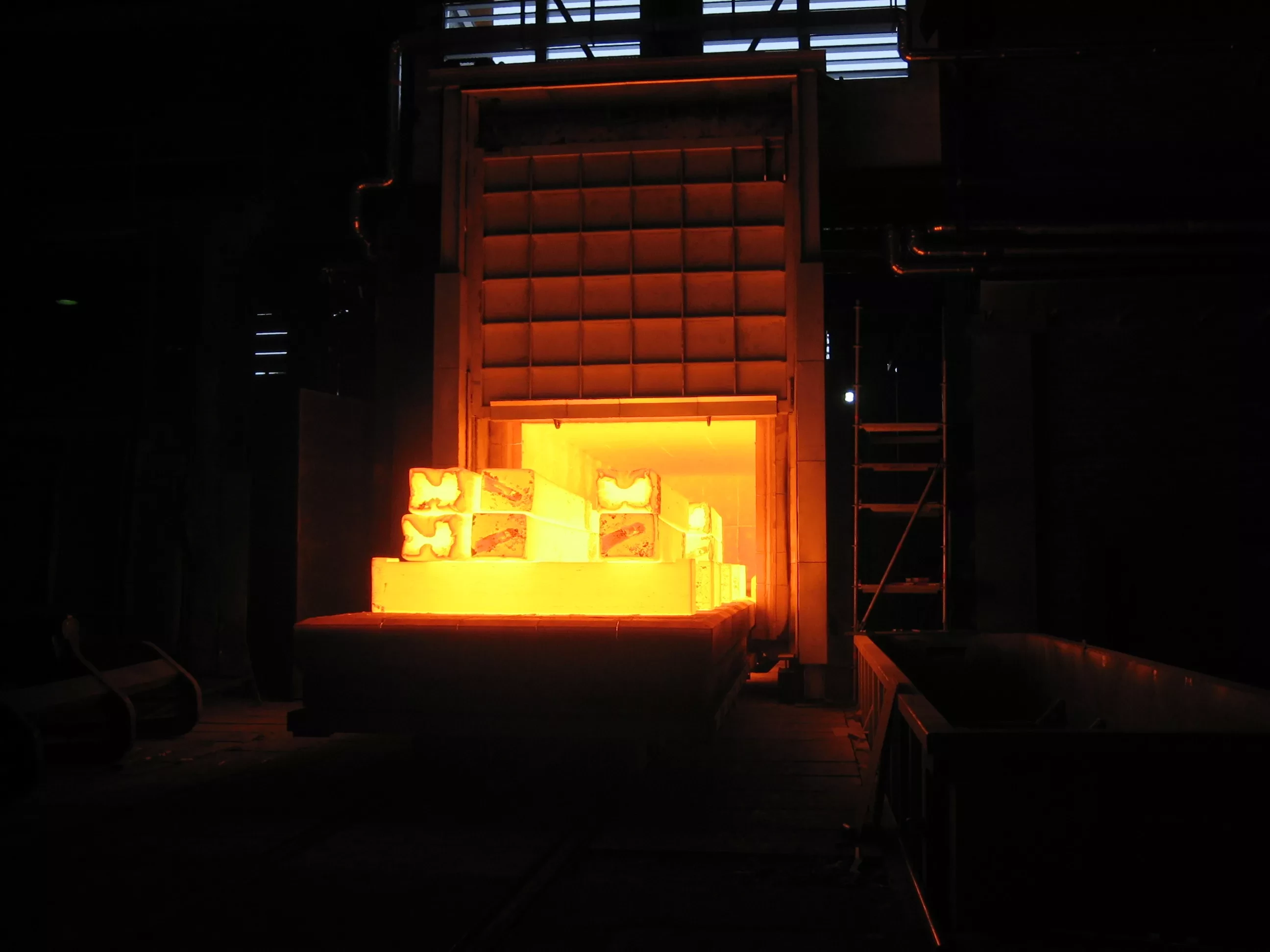
Optimizing your equipments
Calderys refractories for reheat furnaces include customized solutions for every type of furnace up to 1,500°C . Our solutions optimize the overall cost/performance covering installation, manpower, energy consumption and CO2 emissions. We offer local services thanks to an extensive network of Calderys plants around the world
OUR SERVICES
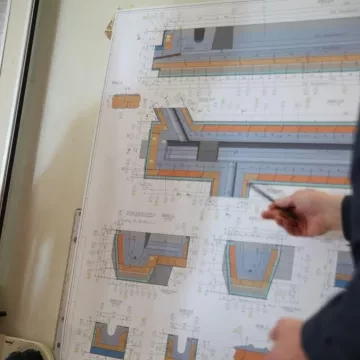
REFRACTORY SERVICES
Calderys offers a full range of services, tied in closely with our world-leading high temperature solutions product lines. We are continually upgrading our services and equipment to ensure that our products are easy and safe to use.
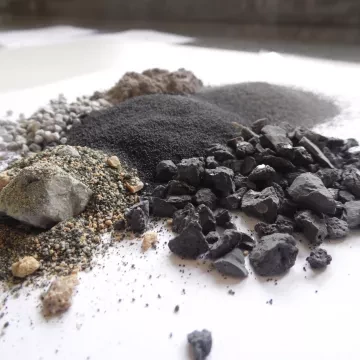
Material selection
Our expert engineers with a deep understanding of your local market, industrial process, and the chemical reactions in your equipment will work with you to identify the best products in terms of performance, lifetime, and cost.
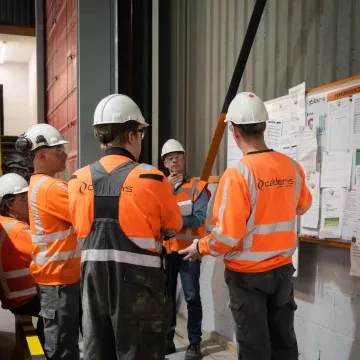
PROJECT MANAGEMENT
Our end-to-end project management services offer you the peace-of-mind you need to focus on your production.
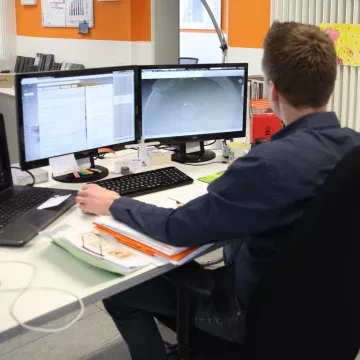
TECHNICAL SUPPORT
Calderys offers full technical support, thanks to a global network of technical experts, acting locally wherever you need it.
Your Equipments

Rotary Furnace
The rotary hearth furnace uses a rotating hearth to move the steel through the furnace, which allows it to be heated evenly. These furnaces face strong thermo-mechanical stresses, where the refractory is critical for a longer and healthier campaign.
All Details
Bogie Furnace
A bogie furnace is used for various heat treatment processes, such as annealing, tempering, stress relieving, and brazing of metal components. Calderys offers refractory solutions that are tailored to the two different types of bogie furnaces.
All Details
Pusher Furnace
The pusher furnace uses a pusher mechanism to move the steel through the furnace. The steel is loaded onto a large tray that is pushed through the furnace by a hydraulic or mechanical system. The main challenges faced by these furnaces are hot erosion and mechanical destruction. Therefore, Calderys has developed specific refractory solutions for these furnaces.
All Details
Walking Beam Furnace
A walking beam furnace uses a series of beams to move the steel through the furnace. They’re able to large volume of steel, and are considered the most advanced type of reheating furnaces.
All Details
Walking Hearth Furnace
A walking hearth furnace is similar to a walking beam furnace but uses a hearth instead of beams. These furnaces are great for medium-size steelmaking processes.
All Details
Soaking Pit Furnace
The soaking pit is a pit-type reheating furnace used for heating or heat preservation of steel ingots, before they enter the next phase of the process.
All Details
Roller Furnace
A roller furnace uses rollers to move the steel through the furnace. The steel is placed on a series of rollers that move through the furnace, allowing it to be evenly heated. Roller furnaces offer a great flexibility in the steel sizes and shapes that are handled.
All Details