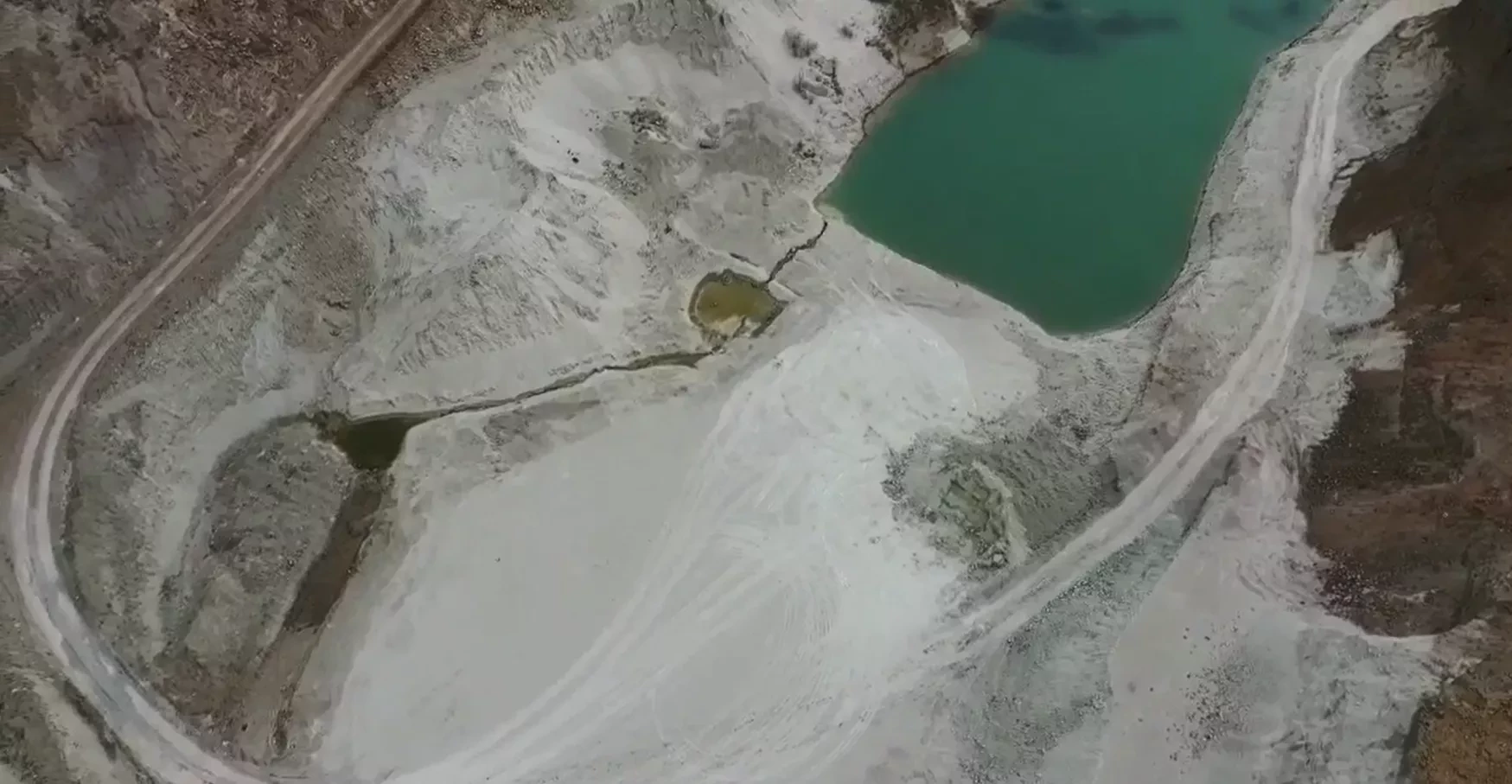
Innovative solutions
We offer a wide range of innovative solutions tailored to customer specifications for molding sand additives that meet high health and environmental safety standards.
Calderys’ extensive mineral and application expertise enables us to supply the best bentonites with high thermal stability and strength. For green engineering blends, our experts formulate specific solutions based on site visits and thorough analysis. For core sand additives, we offer approved organic, inorganic and hybrid solutions. Our special natural and synthetic sands offer very high refractoriness and meet the highest health and environmental safety standards. Calderys’ quarries in Jianping (China) and Taşlık (Turkey) provide us with excellent raw materials, which are processed at our blending sites around the world.
GREEN MOLDING SAND ADDITIVES & CUSTOM BLENDS FOR FOUNDRIES
We have more than 40 years’ experience in processing, blending, and supplying combinations of our high-quality bentonite binders a...We have more than 40 years’ experience in processing, blending, and supplying combinations of our high-quality bentonite binders and lustrous carbon formers to the global foundry industry. Our blends also include treated carbon and lustrous carbon formers to improve casting surface quality, optimize molding sand performance, and minimize additions. In addition to keeping molding costs relatively low with a high level of sand recovery and easy disposal of spent molding materials, bentonite bonded sand allows for the use of modern high-pressure molding lines, which boosts productivity. Our solutions include: bentonite, bespoke bentonite mixtures, slag additives, and protective coatings.
All DetailsIKOBOND® FOR MOLDING STRENGTH
IKOBOND® clay technology is designed for superior durability in high-density molding. The strengths generated speed up sand develo...IKOBOND® clay technology is designed for superior durability in high-density molding. The strengths generated speed up sand development, thereby optimizing consumption. A special blend of bentonite with a small percentage of highly refractory clay improves thermal expansion and reduces the amount of bentonite burned out in the process, resulting in better mold integrity and strength.
All DetailsLUSTROUS CARBON FORMERS
A carbon-containing additive is typically added to bentonite-bonded molding sands to reduce oxidation, minimize sand adhesion to t...A carbon-containing additive is typically added to bentonite-bonded molding sands to reduce oxidation, minimize sand adhesion to the casting during shakeout, improve molding surfaces, and reduce molding defects. It also optimizes the properties and performance of the molding sand.
ANTRAPUR®
Blend formulations can be tailored to fulfill specific client needs. There are several advantages to using “premix” blends. The ad...Blend formulations can be tailored to fulfill specific client needs. There are several advantages to using “premix” blends. The addition of bentonite improves the flowability of the pulverized sea coal, allowing for more accurate dosing in the mixer due to the higher volume added. The main reason for using a blend is safety during transportation and storage. Products classified as hazardous due to their sensitivity and potential to self-ignite require specialized transportation and safety measures during storage. Products classified as explosive require costly ATEX safety facilities at the foundry
All DetailsENVIBOND®
Foundries must produce quality castings consistently and as efficiently as possible while minimizing the impact on the environment...Foundries must produce quality castings consistently and as efficiently as possible while minimizing the impact on the environment and the workplace. This formulation effectively consumes gasses, significantly reducing fumes and hazardous organic compounds. ENVIBOND®: - Reduces the use of sea coal by 30% to 90% - Decreases emissions and odors by up to 95% - Lowers consumption of molding sand binders - Results in cleaner air in the workplace with less need for air filtration - Increases the recyclability of molding sand - Improves casting surface quality - Reduces environmental investments
All DetailsCORE SAND ADDITIVES: ANTRAPEX®
We provide solutions for core sand in the form of additives, to prevent casting defects. We also cover a broad range of solutions ...We provide solutions for core sand in the form of additives, to prevent casting defects. We also cover a broad range of solutions with a variety of products such as organic and inorganic additives: - Special sands (inorganic) - ANTRAPEX®, an additive for cold box core sand that minimizes the risk of veining ANTRAPEX® is non-porous and generally coarse-grained, minimizing losses of core strength. The organic components of ANTRAPEX® improve the casting surface finish during combustion. - Core sand mixtures containing ANTRAPEX® have a long bench life (work time), guaranteeing a consistent process and quality of core produced. - The flowability of the core sand is the same or better with the addition of ANTRAPEX® - ANTRAPEX® has an unlimited shelf life - ANTRAPEX® is not classified as a hazardous substance or dangerous goods - After core breakdown, ANTRAPEX® P in the molding sand acts as a carbonaceous material
All DetailsCOTREX® slag binders
Slag binders are used to clean the surface of the melt prior to pouring. They effectively remove dross and slag from the melting a...Slag binders are used to clean the surface of the melt prior to pouring. They effectively remove dross and slag from the melting and post-treatment processes, ensuring that castings are inclusion-free. The inert nature of the material means there is no reaction with refractory materials in ladle and furnace linings. The high fluidity of our products ensures excellent slag binding power at low consumption. Various particle/grain sizes are available for furnace, transfer, treatment, casting ladle, converter, and induction furnace crucible applications.
All DetailsENVIBOND®
Foundries must produce quality castings consistently and as efficiently as possible while minimizing the impact on the environment...Foundries must produce quality castings consistently and as efficiently as possible while minimizing the impact on the environment and the workplace. This formulation effectively consumes gasses, significantly reducing fumes and hazardous organic compounds. ENVIBOND®: - Reduces the use of sea coal by 30% to 90% - Decreases emissions and odors by up to 95% - Lowers consumption of molding sand binders - Results in cleaner air in the workplace with less need for air filtration - Increases the recyclability of molding sand - Improves casting surface quality - Reduces environmental investments
All DetailsCORE SAND ADDITIVES: ANTRAPEX®
We provide solutions for core sand in the form of additives, to prevent casting defects. We also cover a broad range of solutions ...We provide solutions for core sand in the form of additives, to prevent casting defects. We also cover a broad range of solutions with a variety of products such as organic and inorganic additives: - Special sands (inorganic) - ANTRAPEX®, an additive for cold box core sand that minimizes the risk of veining ANTRAPEX® is non-porous and generally coarse-grained, minimizing losses of core strength. The organic components of ANTRAPEX® improve the casting surface finish during combustion. - Core sand mixtures containing ANTRAPEX® have a long bench life (work time), guaranteeing a consistent process and quality of core produced. - The flowability of the core sand is the same or better with the addition of ANTRAPEX® - ANTRAPEX® has an unlimited shelf life - ANTRAPEX® is not classified as a hazardous substance or dangerous goods - After core breakdown, ANTRAPEX® P in the molding sand acts as a carbonaceous material
All DetailsCOTREX® slag binders
Slag binders are used to clean the surface of the melt prior to pouring. They effectively remove dross and slag from the melting a...Slag binders are used to clean the surface of the melt prior to pouring. They effectively remove dross and slag from the melting and post-treatment processes, ensuring that castings are inclusion-free. The inert nature of the material means there is no reaction with refractory materials in ladle and furnace linings. The high fluidity of our products ensures excellent slag binding power at low consumption. Various particle/grain sizes are available for furnace, transfer, treatment, casting ladle, converter, and induction furnace crucible applications.
All DetailsOUR SERVICES
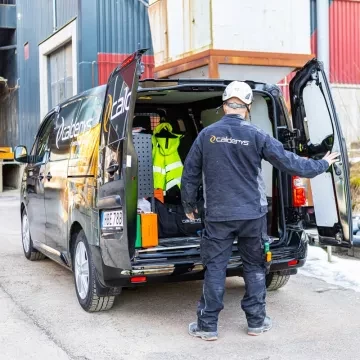
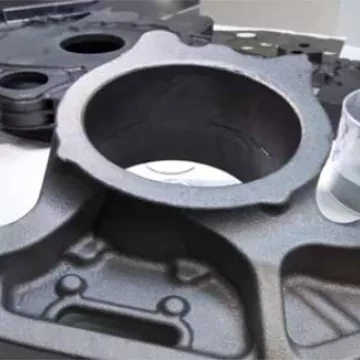
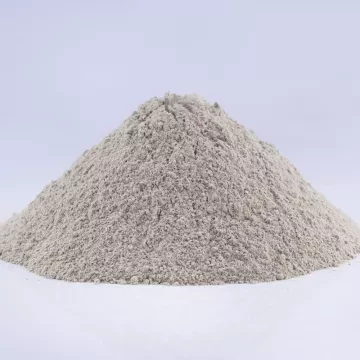
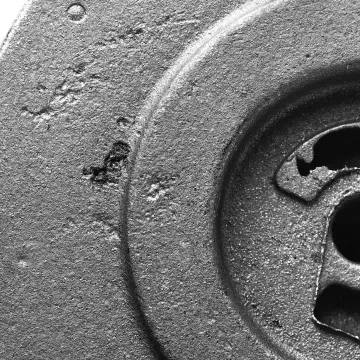
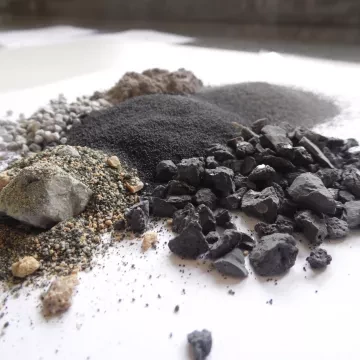
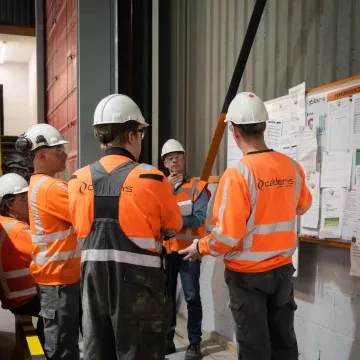
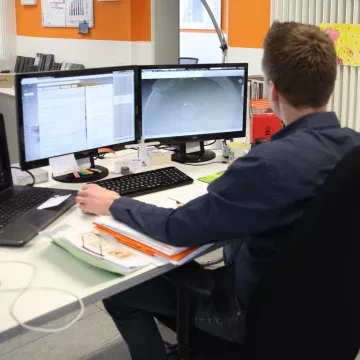