Reducing MgO dependency through alternative ladle lining options
The global refractory market has a high dependency on Chinese sourced magnesia products, of which its supply lines are becoming increasingly restrictive, either through general deterioration of product quality, or more critically, large scale adjustments in trading conditions through new and unforeseen government regulatory constraints and global disruption. However, depending on the steel types being produced, a number of secondary refractory lining options exist that allows for significantly reduced reliance on the MgO footprint of a ladle design.
Dolomite bricks, a high quality alternative that solves shortage challenges
In extreme cases, the restrictions within the MgO raw material market progressively worsen, from the constant irritation of fluctuating price levels and shorter price validity periods on the one hand, to the extremes of such MgO shortages within the market that supplies are only secured through prepayment or sourced at any price. However, by being a manufacturer and supplier of multiple lining technologies, alternative product technology can be gained from a single source. Calderys can provide such alternative lining solutions to alleviate much of the stress associated with high levels of MgO reliance.
As highlighted,the magnesia supply chain has previously undergone restrictions in trade, as recently as 2018, magnesia production was restricted through new environmental regulatory compliance that affected the availability of sinter magnesia in particular. During these times, Haznedar Durer has already demonstrated multiple lining technology capabilities by supporting his customers by switching as much as possible Mg-C bricks to dolomite bricks for their ladle lining. Many of the clients that made such a conversion were happy to remain with the new dolomite ladle configuration, rather than risk being exposed to future market fluctuations. Again, by having a single source of supply, Calderys Haznedar were able to make the switch to the new lining configuration seamlessly, as Haznedar Durer engineers and technical specialists were already fully armed with the steel process parameters and operational conditions and were able to to make such a switch without prior trials.
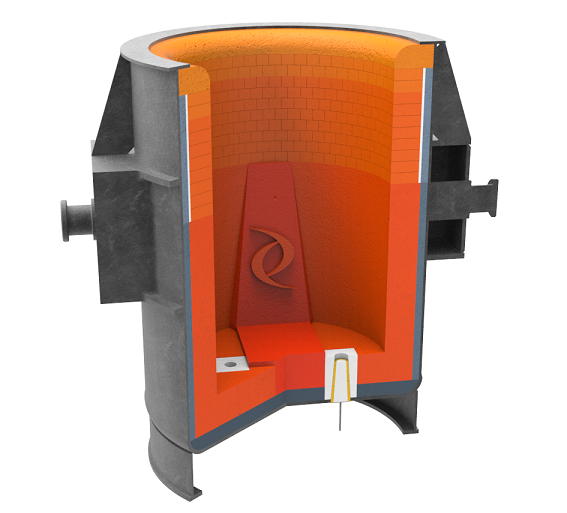
steel quality and process requirements
Multiple refractory lining alternatives secure customers’ production
Depending on the steelmaking process, MgO-C bricks can be replaced by alumina magnesia carbon bricks within the bottom and barrel zones, and, alternatively, to a complete monolithic solution that provides high quality refractory concretes for the barrel and bottom zones, that can be repeatedly repaired to the extent of an ‘endless lining’ concept.
In other instances, magnesia carbon can be exchanged for dolomitic linings, which as well as offering an alternative source of lining, can hold advantages of lower risk of carbon pick up and lower heat losses through a lower thermally conductive lining.
Such lining design flexibility only comes from suppliers with a diverse product portfolio from MgO to AMC, dolomite and high grade speciality monolithics can be a relevant partner for such an approach. Indeed in the case of Calderys and its Haznedar Durer JV, almost every combination that can efficiently combine performance and secure supply can be proposed and designed.
--
Salih Erez, CEO of Haznedar Durer Refractories
Haznedar Durer Refractories is a JV with majority share of Calderys
Craig Willoughby, Technical Development Manager - Iron and Steel Refractory