Tackling health and safety risks with teamwork and good communication
The work environment presents multiple health and safety risks. Whether installing a product at a customer’s site, home working on a computer or operating in a production site, it is important to take the necessary steps to reduce the risk of accidents, injuries and poor mental health.
As the world celebrates the World Day for Safety and Health at Work, David Secret, Calderys Industrial Vice President for Europe, Middle East and Africa, and Bruno Touzo, Science & Technology Vice President, give their perspectives on health and safety within Calderys.
Hi David, Bruno – tell us, what does safety mean to you?
David Secret: To me – and to everyone in Calderys – it means everyone who comes to work leaves in a good shape, with no injury. We need to make sure we place health and safety above everything else.
Bruno Touzo: In terms of science and technology, it also means looking for innovative solutions improving the safety during production and when our products are used by the customers.
What are the risks for employees at Calderys?
David: For plant workers, we have two types of activity: the operations that produce finished goods, and engineering & installation teams working on designs and implementing solutions in facilities of our customers.
We are mainly involved in the Iron & Steel, Foundry and Thermal markets. Often these are big factories, with hot and corrosive environments where many risks are existing additionally to co-activity with other companies. Most injuries are small and concern arms, hands or fingers, and they are due most of the time to light incidents – slips, trips and falls for instance. But this of course is still a matter of concern and requires our utmost attention.
Last risk I would mention is more related to mental health. We must be vigilant with our office employees who have been working from home for months because of the pandemic.
Bruno: Our Science & Technology team is mainly based in plants, so they have to follow the same rules as the other employees. On top of this, they can be exposed to chemical risks.
What is safety training like for someone joining Calderys?
David: All newcomers are trained as part of their induction. On our production sites, they learn about the equipment, the site layout, the main precautions. We have mandatory online training for everyone and, on the process line, new employees spend time learning from an experienced employee.
On an ongoing basis, we have regular management routines – daily shift meetings for instance with the supervisor or production manager, who shares safety news with his/her team, speaking about safety performance, specific mitigation measures to be taken, sharing safety events from other plants, so we can assess if we need to put some corrective actions.
We also have diverse protocols and guidelines to prevent accidents, especially those with the most significant risk. We work within best practices and standards.
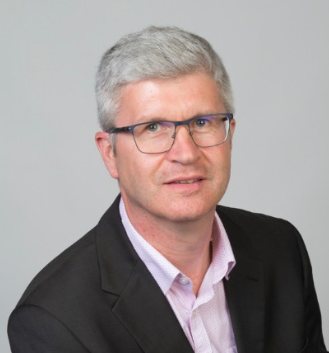
How is the performance within Calderys?
David: Calderys has made huge progress over the past couple of years. Our total injury frequency rate, which is the number of injuries requiring medical treatment per million hours worked, is 3.1%. Two and a half years ago, it was 5.34%. That’s a significant change that our whole team should be proud of. A lot of that is down to good communication. And during critical situations such as Covid-19, it can really make all the difference.
Bruno: There have been no lost-time accidents in S&T over the past years. The objective is to stay at this level. This year we are trying to improve how we monitor and track minor incidents and material damage, and see how we can use this information to improve our safety.
How important is good communication?
David: We have a number of effective communication approaches – safety talks at the start of the day, covering safety precautions and specific actions. These meetings enable people to ask questions.
Visible felt leadership – middle and top managers interacting on the shop floor, encouraging good practices, stopping people if they see unsafe behavior, and recognizing good behavior – is also important. We also have managers who go as frequently as possible to customers’ sites to review tasks, share what they have seen and try to change what is not in line with procedures.
How do you make sure employees are safe when they go and work on a customer’s site?
David: It starts with our commercial approach. We have a system that classifies the companies we are going to work for in terms of their safety maturity and the conditions at their facilities. We will have already assessed the risk, and that will determine what level of safety precautions we will put in place and, of course, whether we go or not. We might not be willing to take a risk in certain environments. Obviously when the installation team goes on site for delivering the project, we have many steps, tools, way to communicate, controls to maintain a high level of safety.
What is Calderys doing to improve products safety and sustainability
Bruno: Everything related to product management is indeed essential and we are constantly working to improve our formulations. We are currently assessing the life cycle of our products with the objective to increase substantially the share of eco-friendly products in our portfolio in the coming years. As part of this effort, we can develop partnerships, such as the one with China Steel Corporation in Taiwan around tap-hole clay and refractory improvement. It's a long-term task that requires perseverance and also good communication and collaboration with our customers to get them on board with these projects.

What effect has the past 12 months had on employees’ mental health?
Bruno: It has been a unique time with some anxiety for our colleagues. Some people are not happy to always be working from home. Some are stressed to come on site. We must be attentive to our employees. And Human Resources have deployed a communication campaign about Covid impacts like stress and anxiety to raise awareness and teach our colleagues how to spot the warning signs and prevent any derives.
What do the next two years hold in store for health and safety at Calderys?
David: Our priority is to progress our maturity culture, and we will look at four specific pillars: leadership and accountability; compliance and continuous improvement; safety behavior; and integrated approach. Regular assessments are done around these points at our sites to find the gaps. We also need to improve awareness and engagement of all people with more training and empowerment, especially of middle management. The work is never finished. We’ve made good progress, but it’s all about continuous improvement.