Calderys Refractory Solutions Support Steelmakers' Green Steel Transition
Transition to green steel: Steel plants are increasingly looking for more sustainable solutions for their processes – specifically ways to reduce their direct CO2 emissions. Refractory suppliers, who are well acquainted with steel plants’ processes, are bringing new solutions to the table.
Innovative solutions to answer environmental challenges
Sustainability is one of the main drivers of change in the steel industry and this is enhanced by the Paris Climate Accord and the Green Deal, both of which are pushing industries to limit their greenhouse gas emissions. This has triggered a multitude of initiatives across the globe.
To reduce their CO/CO2 emissions, steelmakers are progressively adopting hydrogen- and natural gas-based technologies as alternatives to their traditional BF (Blast Furnace) – BOF (Basic Oxygen Furnace) route. The two most promising hydrogen-based technologies are:
- Injection of hydrogen into existing blast furnaces: this would only be an intermediate solution for the iron and steel industries in their green transition, as there is a limitation to the amount of hydrogen that can be injected.
- Hydrogen- and natural gas-based direct reduction of iron ore, coupled with a melting furnace: this process route has the potential to make the future iron and steel industries become carbon neutral.
Both the above processes are highly complex and adapting them to hydrogen and natural gas requires appropriate refractory technologies to sustain the process at designed conditions.
While traditional steel plants produce on average 1.85 tons of carbon dioxide per ton of steel, these new processes, coupled with adapted refractory solutions, enable steelmakers to drastically lower this amount to 0.2 tons of CO2 per ton of steel.
Calderys aims to help its customers in their energy transition, providing them with refractory solutions based on its technical know-how in order for steelmakers to operate at the highest performance in hydrogen-based iron and steelmaking.
Designing refractories linings for hydrogen- and natural-gas based iron and steelmaking processes is challenging because of the high diffusivity of H2 in the material and reactivity of hydrogen with silica from the refractory at high temperature, which, with the increase in H2 concentrations, decreases the physico-chemical properties and the load-bearing capacities.
In order to tackle these challenges, Calderys is developing adapted refractory solutions to its customers, and is even going further by partnering with various laboratories. Together they have launched several studies to better understand the high temperature interactions of hydrogen with different refractory materials. In one of the studies, we subjected seven different refractory materials to a high concentration of H2 for up to 240 hours at an elevated temperature. It was observed that there was a substantial decrease in the Young’s Modulus(1) of the materials. In another study, the modeling of a DRI showed the thermal stresses generated by the chemical reactions inside the process, helping Calderys to understand which type of refractory material is best adapted to different parts of the DRI reactor (see image).
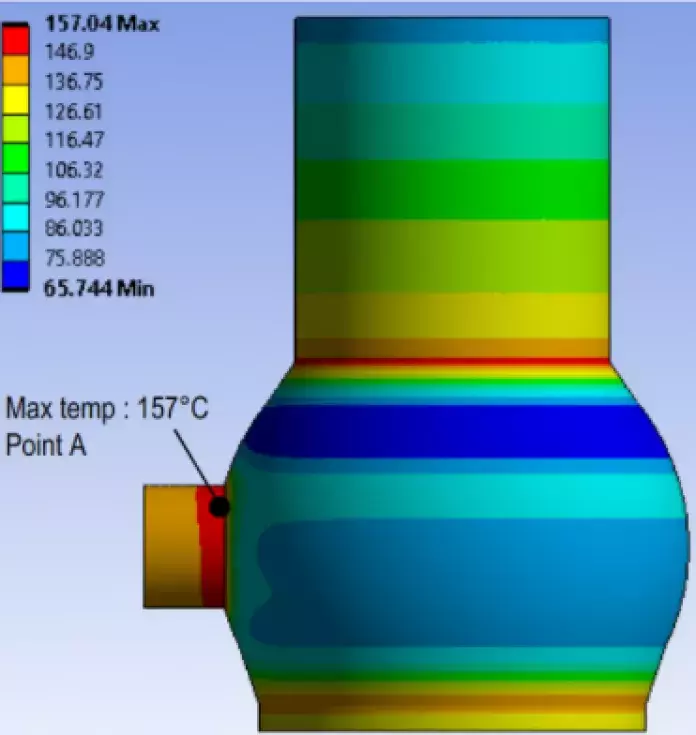
A number of other studies are underway to understand the complex high temperature interactions of hydrogen with refractories. This will help us design even better refractory solutions for the iron and steel industries' evolving needs.
--
1 Young's modulus is a measure of the ability of a material to withstand changes in length when under lengthwise tension or compression.